Citric acid can be used to produce transparent, rigid and heat-resistant bioplastics, which could be used for ketchup bottles, but also in more high-tech industry.
Despite the development work that has gained momentum in recent years, the fields of application for bioplastics have been relatively limited. They are used for producing plastic bags, for example. “The difficulties of obtaining rigid plastics from biological raw materials are already written into its structure. For example, while there is almost no oxygen in fossil raw materials, its level in biological raw materials reaches 40 per cent,” explained the senior research fellow in organic chemistry at the University of Tartu, Lauri Vares, who led the research.
High oxygen content makes the polymers produced from it soft and makes them absorb water. Vares and his colleagues saw the solution in adding elements that would increase the rigidity of the structure, i.e. cyclic molecules.
“The process is not very complicated, as there are no stages that would require the substances to be thoroughly cleaned. We think this could also be done on a large scale. At the same time, the obtained polymer can be processed in the same devices used for processing the currently available fossil raw materials. This would make its implementation that much easier,” expanded the senior research fellow.
In the experiments conducted so far, the produced polycarbonate starts to gradually soften at about 100 °C. The produced polycarbonate is liquid and thus conveniently processable starting from about 170 °C. Unlike most other bioplastics, it starts degrading only after reaching 350 °C.
“Thanks to its good temperature tolerance and stability, the material should be relatively easy to reprocess,” noted Vares. The environmental friendliness of the material could also manifest in another way. Although no respective tests have been conducted yet, the novel bioplastic should be relatively resistant to the degrading effect of solar radiation. This in turn reduces the risk for the formation of microplastics.
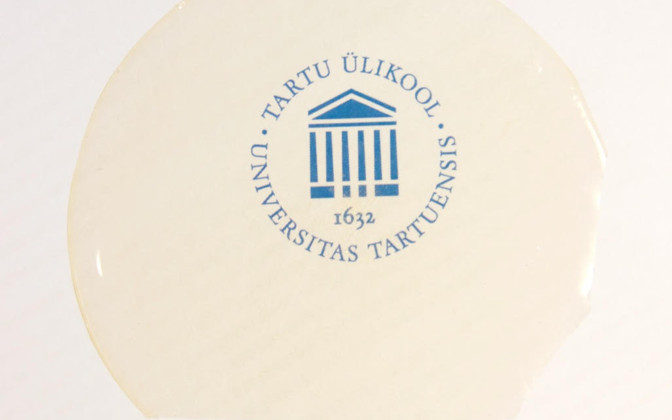
On a broader scale, the produced bioplastic could be suitable for any application requiring a stronger plastic with good transparency and a higher temperature resistance. “For example, it could be used in hot fill ketchup bottles, but would also be suitable for more high-tech applications, such as in the automobile or aircraft industry,” said Vares noting some examples.
As the next step, the working group is planning to see whether the citric acid used as the raw material could also be produced using wood sugars in addition to the agricultural raw materials. Among others, the sugars from the wood fractionation demo plant being developed by Graanul Invest are going to be tested in cooperation with Lithuanian and Norwegian partners. Ideally, this could reduce the mark left on the environment.
“In the process, we will assess the environmental impact from raw materials to the final product, to see if and how much we can save in comparison with the existing solutions. This is very important, as the prefix ‘bio-’ does not necessarily mean that it is something great or environmentally sustainable,” said the senior research fellow.
There is also room for development in terms of increasing yield. This comes mainly down to the mass effect. Currently, the diameter of the larger pieces of plastic produced in the lab has been approximately 10 centimetres. Producing polymers in semi-industrial devices is easier and it is easier to check the polymerisation parameters.
Vares and his colleagues are also planning to see whether the single elements used this time – monomers – can also be used to produce, for example, polyesters, polyurethanes and other similar materials. The senior research fellow conceded that their current price would almost definitely surpass that of the existing fossil materials. However, this could change on a larger production scale and if the regulations concerning the use of fossil raw materials become more stringent.
The research was published in the journal Green Chemistry.
The translation of this article from Estonian Public Broadcasting science news portal Novaator was funded by the European Regional Development Fund through Estonian Research Council.