Every second, 73 pairs of jeans are sold all over the world. The production of one pair of jeans uses 7000 litres of water. One way to make the denim industry more sustainable would be to create more durable fabric. An Estonian PhD student worked on finding the best suitable fibres for denim and the optimal parameters for environmentally friendly laser fading.
“It takes a lot of water, energy, and chemicals to produce jeans,” says the recent PhD student Nele Mandre. You can’t calculate the overall environmental footprint of jeans because the way jeans are produced and processed can vary. Even the same method of production can vary in the time it takes to complete the process. “For example, during stone and enzyme washing, the amount of energy and water spent is measured by the amount of time spent on the process itself, which can take either half an hour, 45 minutes or an hour,” explains Mandre.
Even though it takes a lot of resources to produce just one pair of jeans, they’re not worn for very long if they’re bought from a fast fashion chain. Some people never even wear jeans bought during a sales campaign, and it is generally expected that one pair should last just two to three years. “Two to three years is the optimal time people expect,” says Mandre. “If I exceed their expectations, then that’s already an achievement in my eyes.”
In her recently completed PhD, she searched for a durable denim fabric, developing in the company Põldma Kaubanduse AS under the Denim Dream retail chain. Mandre’s goal was to find a good way to laser fade durable denim fabrics while also damaging them as little as possible and not losing the visual appeal and comfort. “Since my topic was tied to sustainability, I think it’s essential to lengthen the durability of the product,” she says.

An expense in the name of the client
According to Nele Mandre, 2.3 billion pairs of jeans are sold every year and 73 pairs every second. It takes as much water as showering 287 times to produce one pair of jeans. “About 27 million tons of cotton is produced per year, and about 11 million of it is used to make clothes,” she explains. “This topic needs to be addressed since the environmental footprint of a single pair of jeans is enormous.”
According to her, the main component in a pair of jeans is always cotton. Jeans are also recognised for their indigo-blue colour and their functional cohesion. “Functional cohesion means that if we look at the surface of the fabric, then we can see diagonal stripes going all the way across the jeans,” explains the recent PhD student.
Initially, denim made from cotton was stiff and a durable fabric for workwear. But today, clothes made from so-called raw denim are not sold anywhere because, according to Mandre, no one would buy them. “Denim is always being developed and improved – according to demand,” she remarks. Modern jeans are thus multi-component, meaning they consist of multiple fibres.
“The main component is still cotton, but other fibres are added as well, as this is what the client wants.”
For example, the fabric developed by Mandre consisted of polyester, viscose, elastane, and cotton. Elastane gives jeans their elasticity and makes the jeans more comfortable for the person wearing them. Polyester makes the fabric more durable, viscose adds shine, and the fabric feels more silky to the touch. “The main component is still cotton, but other fibres are added as well, as this is what the client wants,” explains the recent PhD student.
The laser fading, which she studied, primarily affects the colour of the denim. The longer the indigo-blue fabric is faded, the lighter it gets. “It needs to be said that any kind of bleaching method damages fabrics, whether it’s laser fading or stone wash,” admits Mandre. That means that processed fabric will be more brittle. “If we didn’t do it, we wouldn’t have any clients who would buy the product,” she adds.
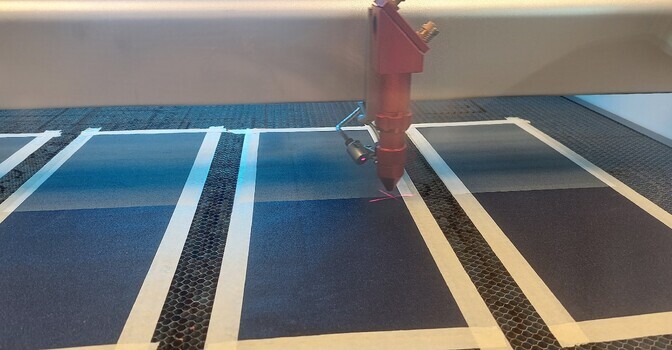
The goal was to find laser fading parameters that would both keep the appearance and improve durability. Mandre instantly wanted to find out where the optimal strength ends. “I set minimum requirements for durability,” she explained. “Clothes don’t usually have strict minimum requirements, but I used the requirements recently developed in Belgium for my basis.” She then used different laser fading parameters on her fabrics and also changed the output power and speed of the laser fading process.
“I found two parameter combinations; one resulted in a slightly lighter tone and the other in a slightly darker one,” said the recent PhD student. Despite the fading, both combinations met the minimum requirements for strength and abrasion resistance, according to Mandre. “Abrasion resistance was reduced by 50% compared to raw denim, but I definitely can’t say the result was so bad that it wouldn’t last a normal wear.”
A wise investment is worth the cost
Upcycling is what’s usually meant when sustainability is mentioned, but according to Nele Mandre, the phrase has a much broader meaning. “I handled this topic from a different perspective,” she explains. “For me, it was vital to raise the quality and durability of the product.”
According to Mandre herself, the fabric was developed based on the set requirements and knowledge. In contrast, the effects of fading are not apparent when it comes to fast fashion chains. “I don’t think anyone has tested them to ensure they meet the standards. This is why I think that perhaps fast fashion chain products have been faded too much,” she says. Therefore, the clothes break more easily and end up in a dumpster quite soon.
The fabric developed by Mandre can still be upcycled when its wear cycle has ended. “Upcycled multi-component textile fibres are good for producing many new materials, whether by spinning them into yarn again or using them in more technical materials, such as building or interior materials,” she says.
As an Industrial PhD student, Mandre’s goal was to bring her product to life. “I find that the results I’ve found during this research need to be put into use.” She plans to create a collection from her new sustainable sustainable fabric under the Denim Dream brand. “My next goal is to turn the theoretical work into practical work and produce things made from the developed fabric,” says the recent PhD student.
The PhD student Nele Mandre in the Department of Materials and Environmental Technology defended her doctoral thesis “Effect of Fibre Content, Structural Parameters, and Laser Fading on Durability and Aesthetic Properties of Multicomponent Denim Fabric” (“Kiulise koostise, struktuuri parameetrite ja laserkulutuse mõju mitmekomponentse teksakanga vastupidavusele ja esteetilistele omadustele”) on 29 August at the Tallinn University of Technology. The industrial doctoral thesis was made in cooperation with Põldma Kaubandus AS. The work was supervised by the senior lecturer Tiia Plamus and by the tenured associate professor Andres Krumme from the Tallinn University of Technology.
Written by Airika Harrik. This article was originally published on the Estonian Public Broadcasting webpage Novaator.