Table of Contents
Two sister projects led by researchers at the University of Tartu aim to develop new methods for separating rare earth metals at scale, technologies that, if successfully implemented, could alter the way such metals are obtained from a variety of raw materials. Such technologies could also impact the Estonian economy, as rare earth metals are in demand for use in magnets and microchips and are essential components in computers, electric cars, robots, photovoltaic panels and wind turbines.
Both projects commenced earlier this year. The first, led by Enn Lust, professor of the Institute of Chemistry at the University of Tartu, is called “Extraction of Rare Earth Metals from Natural Ores by Ionic Liquids.” The project has a budget of nearly €1.4 million, began in January, and will run through the end of 2028. The second is called “Electrochemical Deposition and Nano-powder Production of Rare Earth Metals” and has a budget of around €560,000. Led by Ove Oll, a researcher in the department of physical chemistry, it also started in January and will end in ’26.
While officially separate, Lust said both represent “one common project, divided artificially into two parts,” as there is no possibility to deposit rare earth metals without using novel extraction and separation methods first.
“His project is the starting point, where you get the raw material, do the initial purification and separation chemically,” explained Oll. “I will start on more concentrated material, separating out each of these elements one by one using electrochemical deposition.”
Boosting Innovation with €354M from the Just Transition Fund
The twin projects have been funded through Estonia’s Just Transition Fund (JTF), which has invested €354 million from the EU’s JTF to support investments in the economy of Ida-Viru County in northeast Estonia, long a center of mining, manufacturing, and rare-earth processing.
The projects were two of 22 awarded to research groups at the University of Tartu and Tallinn University of Technology (TalTech) both of which have a presence in Ida-Viru: TalTech maintains its Virumaa College in Kohtla-Järve while the University of Tartu has its Narva College in Narva.
As Oll noted, the Just Transition Fund targets regions in Europe where fossil fuels have been produced in the past but where production is declining and new ideas are necessary. Ida-Viru fits the bill, as its industries have been operational for a century or more. Ida-Viru is also a hotbed of activity. It’s the home of Silmet in Sillamäe, a rare earth processing firm, owned by Toronto-based New Performance Materials. NPM is also investing €100 million to set up a magnet factory and R&D center in Narva. The JTF has invested about €18 million in the project.
“It is critical for Europe’s infrastructure to produce these kinds of technological resources,” Oll said. One eventual user of the technologies under development at the University of Tartu could be a company or companies in Ida-Viru, he noted. The JTF-funded projects will end by 2029, and other than scientific articles and new doctoral students, there will be a commercial output.
“There are many candidates we can work with,” said Oll, “and there are many companies working on metals in Ida-Virumaa. The main thing is that production would be in Ida-Viru.”
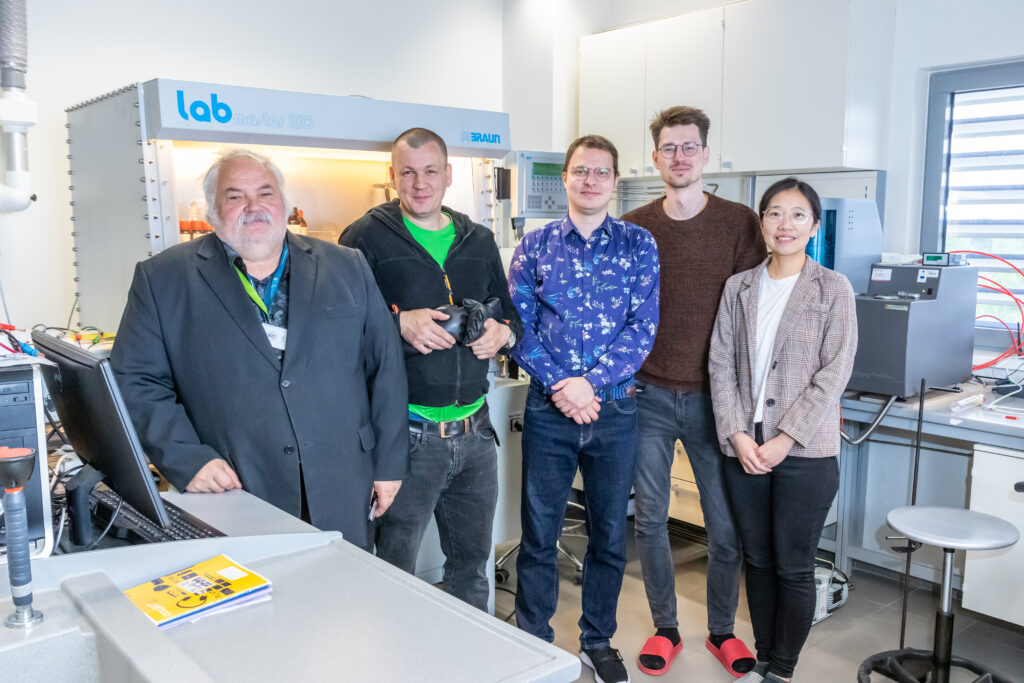
Prospecting for Rare Earth Elements
The names of the rare earth metals in question may be unfamiliar to some. There’s lanthanum, a soft, silvery white metal; cerium, a similarly soft, silvery metal; neodymium, harder, but malleable and also silver in color; and ytrium, a silvery-metallic metal. These metals are used in various areas of modern technology, such as in hydrogen storage devices, super magnets, and in DC motors, which are components of wind turbines and electric cars.
Processes to extract these metals exist but require many steps and rely on solvents and specific sometimes flourinated materials that are hard on the environment, which is one reason that China, where environmental standards are less stringent, has emerged as a leading provider of such metals.
According to Oll, the raw materials exist in Estonia for processing. These might be domestic raw materials such as the waste from Estonia’s phosphorite ore extraction industry, or materials imported and processed at NPM Silmet. The challenge now is to implement new approaches to extract the metals of interest from these materials in an environmentally friendly manner, while reducing the amount of steps necessary to undertake the extraction. The group at the University at Tartu has for years been working on such methods and will now work to develop them further.
Central to the envisioned approach is the use of ionic liquids and ionic liquid mixtures synthesized with suppliers or on site in Tartu, followed by the application of an electrochemical extraction technique. The latter relies on the use of the metal bismuth as a surface on which the rare earth metals are deposited and form alloys. These alloys are then heated in clean hydrogen to recover the bismuth as well as to produce rare earth element powders. The extracted rare earth metals will then be available for use in the production of solid oxide fuel cells, hybrid supercapacitors, direct methanol fuel cells and thin-film H2 storage devices, for example.
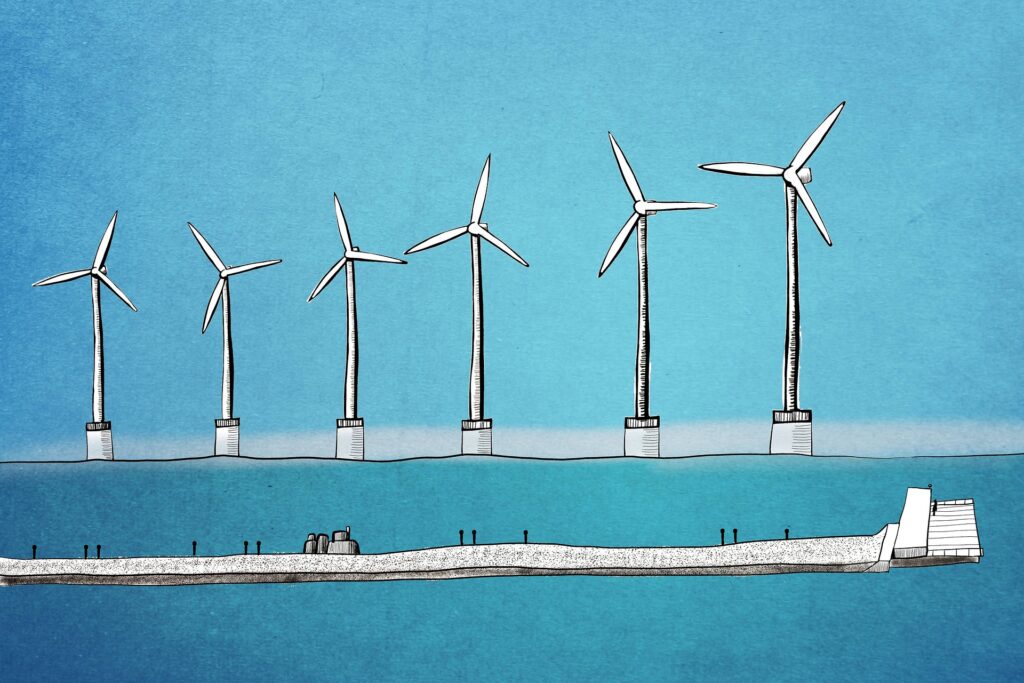
Purifying Rare Earth Metals with Fewer Steps
At the University of Tartu, Oll noted, researchers are also developing high-temperature electrolysis cells that rely on such rare earth metals. It can take five rare earth metals to make one device, and the metals have to be very pure in order for the devices to be long-lasting and viable.
“Just having 99-percent purity could be terrible because if 1 percent is chromium or silica, it’s not going to work,” said Oll. “The purity has to be extremely high and that’s why novel two step-chemical separation and electrochemical deposition cycles have been needed to achieve it.”
He noted that the approaches outlined at the University of Tartu do not rely on fluorinated materials and use less steps than traditional methods. “With a novel chemistry approach you can reduce the amount of steps because it’s more specific,” said Oll.
Ideally, the process would involve about a dozen electrochemical separations. However, he said there are challenges, as the metals are similar. “You have to be able to make the difference between two very similar elements so that you can separate them,” he said.
Currently, months into both projects, Oll said they are at the proof of principle stage. How the methods developed are ultimately applied though will depend on what the source material is. If the Estonian government decided to restart the mining and processing of phosphorite ore, then it could be considered as a raw material source. But industrial waste is another candidate, both produced within Estonia as well as material that could be imported.
“A lot of different ores around the world have rare earth elements in them as the separation is too expensive,” said Oll. “We may have more resources to consider for rare earth elements.”
This article is written by Justin Petrone. This article was funded by the European Regional Development Fund through Estonian Research Council.
If you’ve got a taste for innovation and crave juicier insights, sink your teeth into our article on how science is boosting meat quality – because better bites start with smarter science!