Table of Contents
Researchers from TalTech Virumaa College have received a utility model certificate from the Patent Office for an innovative pyrolysis method that allows hydrogen to be produced from old packaging and wind turbine blades.
Recycling non-mechanically processable packaging is one of the biggest environmental challenges today. These are known as composite materials and include glued or fused plastic, foil and paper.
Such packaging is usually made up of multiple layers and materials, including glued or fused plastic, foil and paper. The layering gives the packaging strength, durability, density and protection against external factors. Unfortunately, this makes recycling the packaging much more difficult.
Wind turbine blades pose an equally serious challenge. They are made from reinforced composite materials, such as polymer resins strengthened with glass or carbon fibres. These materials ensure the blades are strong and durable, making them ideal for extreme weather conditions. However, for the same reason, recycling wind turbines blades is extremely difficult.
What makes the recycling of composite materials difficult is that each layer has different physical and chemical properties. Separating them requires complex and costly technology. While it is possible in theory, only a small part of this waste actually gets recycled. This is due to limited infrastructure and complex technology, which makes recycling economically impractical for most companies.
With the growing number of wind farms and the increasing use of composite materials in various industries, the challenge of disposing of them is becoming even bigger. Wind turbines typically last 20–25 years, and the number of blades to be decommissioned is steadily and significantly increasing. In the coming decades, tens of thousands of blades are expected to be disposed of. Most of them end up in landfills, where they take up a lot of space and pose long-term environmental risks. Wind turbine blades affect the environment for centuries.
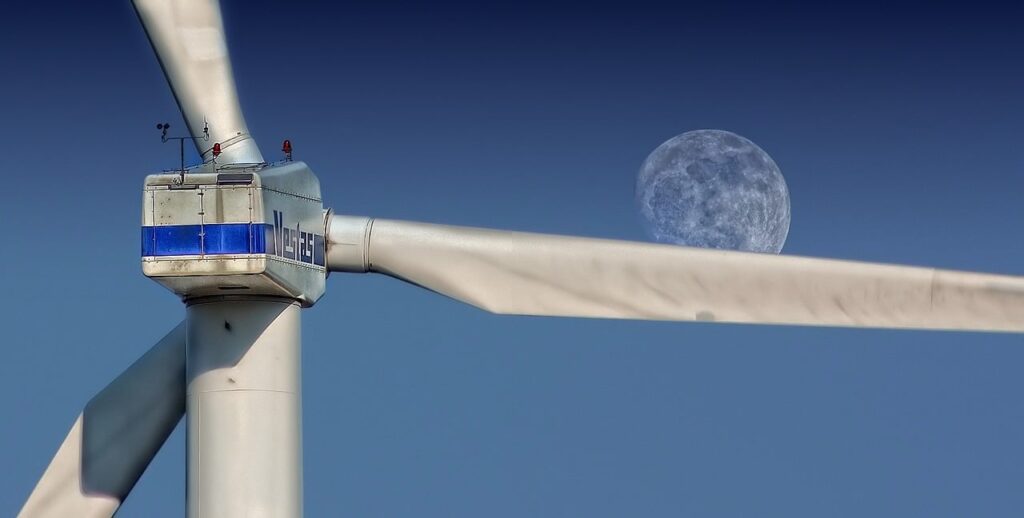
The solution? Two-stage hydrogen production
A two-stage pyrolysis method has been developed at the Laboratory of Fuels Technology at TalTech Virumaa College. This will help overcome the challenges of recycling composite materials, packaging and various types of bio-waste.
In two-stage pyrolysis, waste undergoes thermal treatment to obtain a synthesis gas with a high hydrogen content. Unlike traditional pyrolysis or gasification, this process is more complex. The method involves two stages of heating and decomposition, making it efficient for processing different types of waste.
The main advantage of two-stage pyrolysis over traditional gasification is the absence of air in the process. This prevents unwanted side reactions, such as oxidation, and minimises the carbon monoxide (CO) and carbon dioxide (CO2) content in the synthesis gas. As a result, it produces a much cleaner gas with a higher hydrogen content, which can be used for energy and industrial purposes, including electricity generation.
Generating electricity from hydrogen gas using fuel cells can significantly improve energy efficiency. Since this process produces practically no harmful emissions, it is a key element in transitioning to clean technologies and reducing dependence on fossil fuels. Additionally, hydrogen is a valuable raw material in the chemical industry, where it is used in the production of ammonia, methanol and fertilisers.
The utility model certificate encourages further development
Research carried out at the Laboratory of Fuels Technology has shown that processing one tonne of packaging and composite material waste can yield about 1200 m³ of synthesis gas, of which 800 m³ is hydrogen. Processing the same amount of wind turbine blades produces about 350 m³ of synthesis gas, of which 250 m³ is hydrogen. The lower amount of synthesis gas output from turbine blades is due to their composition (glass and carbon fibres do not decompose when heated).
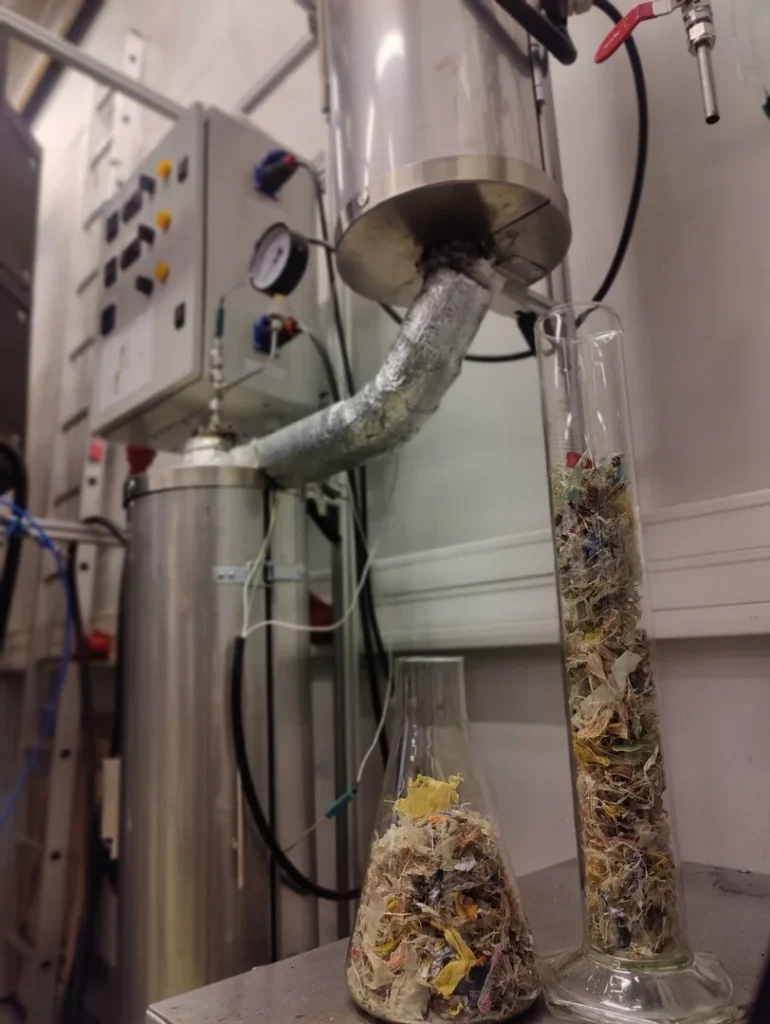
Future research will investigate the uses of solid residue from two-stage pyrolysis, such as in the production of filters or fuel cells. The remaining glass fibre can be added to concrete mixtures to improve the quality of the concrete and reduce the need for other fillers or reinforcing materials in the concrete.
In October this year, the Patent Office granted a utility model certificate for a method of producing synthesis gas by pyrolysis of organic raw materials using solid heat carriers.
Estonia and the European Union have set up a support measure ‘Support for increasing the knowledge intensity of business in Ida-Viru County: developing the provision of research capacity in Ida-Viru County for the creation of a research and development network’, which will fund research on the use of waste unsuitable for mechanical recycling in the chemical recovery processes.
This article was originally published on the webpage of Tallinn University of Technology (TalTech) in their publication TRIALOOG. Author: Olga Pihl.
If this glimpse into chemistry has sparked a reaction, don’t let the curiosity fizzle out! Bond with our next article for more explosive discoveries and read more about how University of Tartu Researchers Developing New Methods to Extract Rare Earth Metals!