Can robots be predesigned for unpredictability?
While today’s large language models adapt situationally on the fly, their bodies remain fixed. They are either optimized for a specific task or built into a one-size-fits-all principle that rarely excels. But what if a machine could develop any structure demanded by its situatedness, right when and where it’s needed?
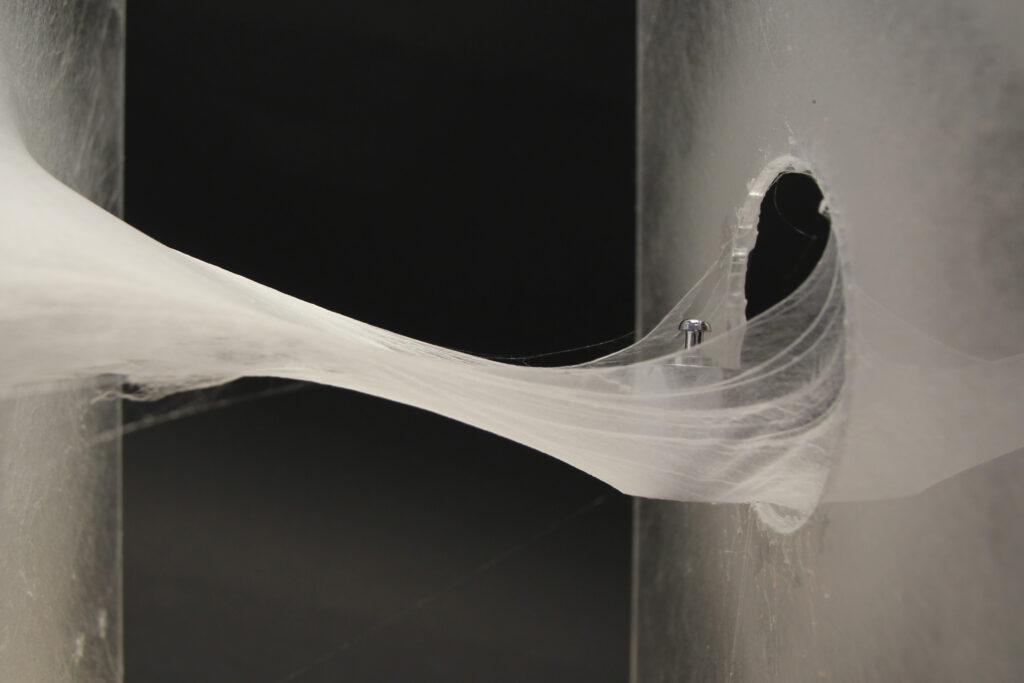
Researchers at Tartu University’s Institute of Technology have unveiled a robotics concept that redefines adaptability by literally weaving its body on demand, much like spiders spin their webs. By extruding a heated polymer solution that cools into fine fibers, the robot creates custom components in situ. The result is a dynamic melding of machine and environment! A seamless transition that bypasses the rigid separation of traditional robotic design.
In a series of experiments, the team showcased the robot’s remarkable ability to operate in complex environments. In one demonstration, the machine spun a continuous, flexible fiber network across a simulated debris field, building its own bridge over obstacles indifferently whether the path was lined with razor-sharp glass shards or soft bird feathers. In another test, the robot spun itself a fibrous “limb” to gently retrieve a fragile flower, illustrating a level of dexterity that predesigned embodiments cannot match.
The team demonstrated indiscriminate adhesion and anchoring of in-situ spun webs on virtually any substrate, regardless of shape, material, or state of aggregation. Much like spiderwebs, the synthetic web leveraged both physical adhesion and mechanical entanglement to secure itself to a broad range of supports.
In experiments, the web successfully anchored on challenging surfaces such as Teflon, a sponge saturated with mineral oil, and a waxy plant leaf.
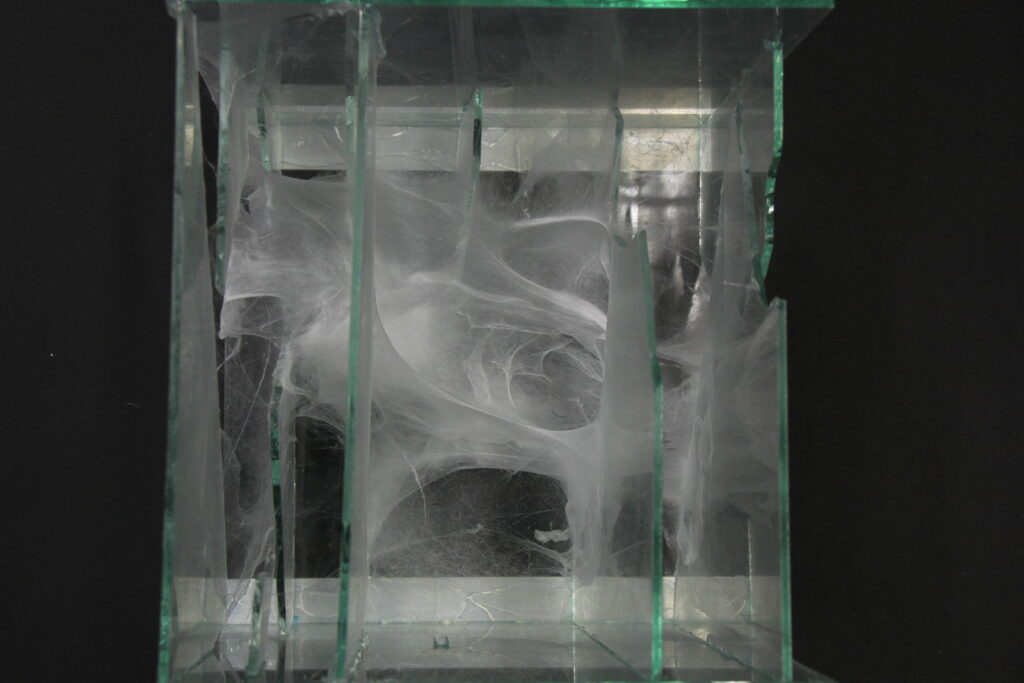
“Our approach takes a cue from spiders as nature’s ingenious engineers, yet we found a loophole that lets us sidestep the limitations and excessive complexity of directly imitating spiders,” said Marie Vihmar, lead author of the study published in npj Robotics.
With a background in design studies, Vihmar brings a fresh perspective on non-anthropocentric design and how the form and shape of materials create functionality, while the senior author Indrek Must, who is trained in material science, ensures the technological robustness of the innovation.
This interdisciplinary collaboration converges design thinking, material science, and robotics, yielding insights and solutions that remain elusive to conventional approaches within any single discipline.
By exploiting the self-assembling properties of polymer fibers, also observed in cast-off kiting silk of spiders in nature, the team has created a system that dynamically assembles itself to meet the immediate challenges of unpredictable environments. This not only broadens the scope of robotics in disaster relief but also rethinks how machines interact with the world.
This contribution paves the way for robots that don’t simply adapt to their surroundings, but actively transform them! From search-and-rescue operations in disaster zones to adaptive construction methods that seamlessly merge machines with landscapes, the technology challenges conventional industrial thinking. Instead of forcing the environment to accommodate rigid, predesigned systems, this innovative “forest thinking” approach empowers machines to grow and evolve on the spot.
Supported by the Estonian Research Council, this research marks a significant step forward in the convergence of biological inspiration and robotics. Introducing an era where machines are not static tools, but dynamic entities capable of reinventing themselves not only mentally, but also physically.
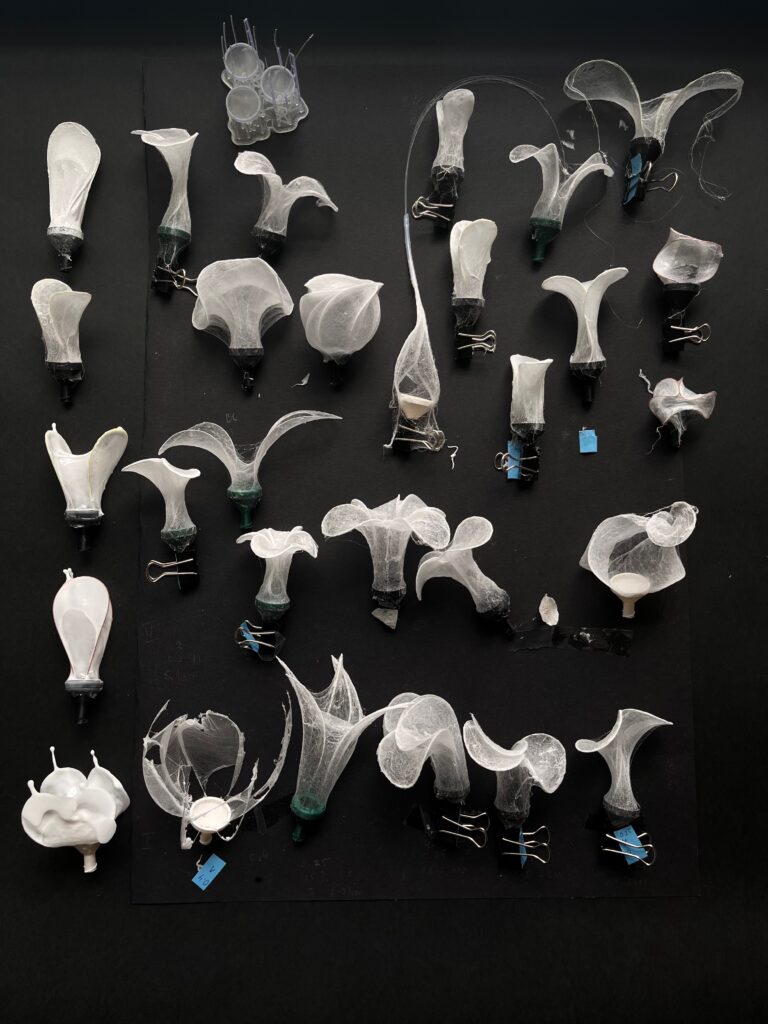
DOI 10.1038/s44182-025-00019-2
Expert Contact
Indrek Must
University of Tartu, Institute of Technology
indrek.must@ut.ee
This article was sent to us from University of Tartu and was originally published on the EurekAlert webpage.
If this peek into robots has you feeling programmed for more, don’t hit shutdown! Charge ahead to our next article and read more about how Robots can now walk through muddy and slippery terrain, thanks to Moose-like feet!