Table of Contents
Transforming lower-quality wood into high-quality material
While the resource-poor world is currently concentrating on lower-quality wood, TalTech scientists’ research confirms that inferior wood can indeed be processed into high-quality wood.
This was revealed by the recent findings of a project led by Professor Jaan Kers of TalTech University and supported by the Centre for Environmental Investments SA named “The potential use of Estonian underused wood species in new veneer-based products”. The removal of lignin could be considered one of the success factors.
According to Kers, four wood species were primarily used in the project: birch, aspen, black alder, and grey alder. “Birch was a high-quality reference material within the project with which other, lower-quality wood species were compared,” said Kers.
The investigation began by identifying the physical characteristics of the mentioned wood species. “An experimental process of hardwood densification was chosen to improve their mechanical properties, which could easily be used in production using already existing equipment,” according to professor. Glulam and veneer were the two main wood-polymer composites investigated during the experiments.
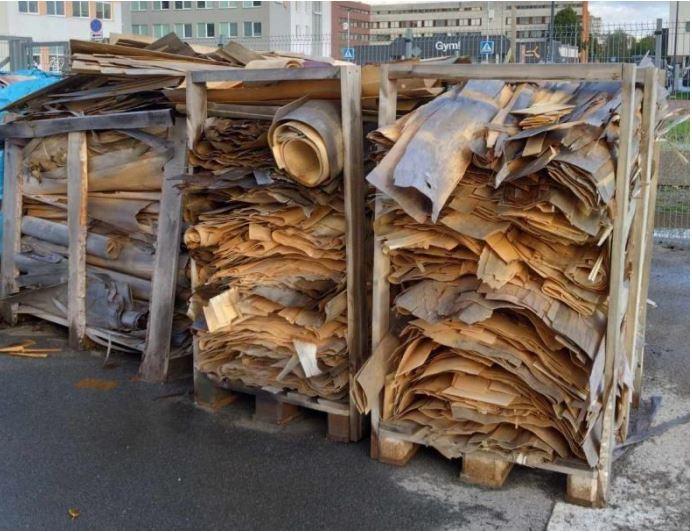
Lignin as a key factor
What did the results indicate? An investigation of the wood densification process and the resulting veneer properties revealed that partial lignin removal from the wood can significantly improve densification while preserving the integrity of the wood cells.
Kers added that because lignin had been partially removed, densified wood samples had better dimensional stability after being exposed to moisture or soaking in water, followed by drying in an oven. “Combining lignin removal and high moisture content during densification process proved to be beneficial, as it reduced recovery from 100% to 70% of total dimensions.”
These findings revealed that lignin played an important role in wood cell wall deformation during densification, as well as in the restoration of the cell wall to its original shape after repeated wetting. As a result, the densified wood’s ability to recover its original dimensions was reduced when moistened. “Since dimensional recovery still occurs, the effect of lignin remains small in this regard, we need to study the effects of other wood components as well,” noted Kers.
In addition, the researchers discovered that densifying low-quality hardwood veneers and applying them to plywood faces significantly increases the plywood’s overall density. “However, only black alder plywood with all compressed veneers achieved a higher density than birch plywood” stated Kers. There was also a strong positive correlation between plywood density and screw withdrawal capacity, which stayed the same with all the plywood types within the different wood species. “These results support the hypothesis that increased plywood density with only surface veneers densified will lead to significant screw withdrawal capacity improvement.”
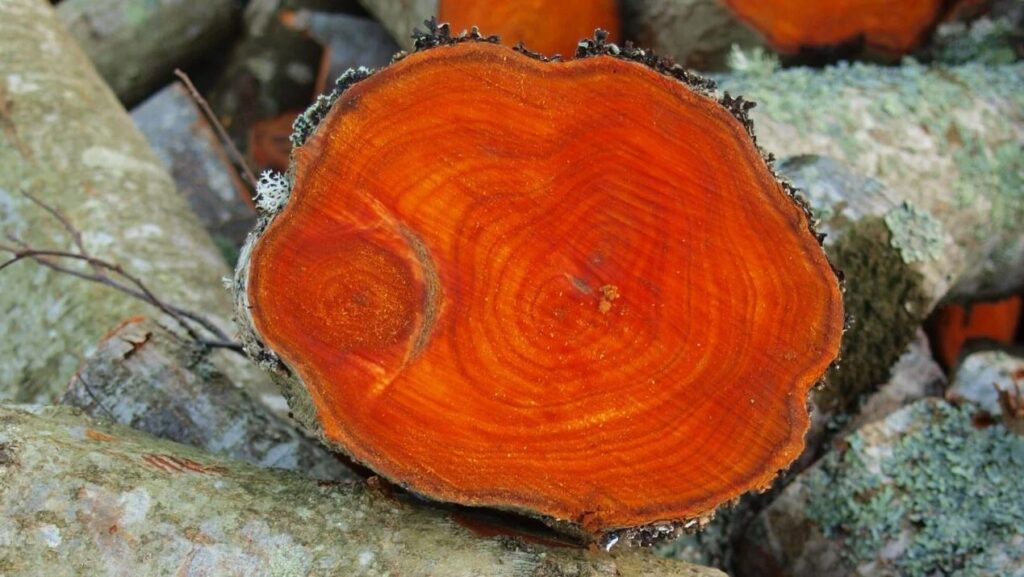
Which type of wood has the highest screw withdrawal capacity?
Screw withdrawal capacity remained the highest for undensified birch plywood and black alder plywood with all densified veneer layers. However, when compared to birch plywood, the densified surface veneers significantly increased the screw withdrawal capacity of the aspen and black alder plywood. The conclusion is that the density of the plywood faces has a significant impact on the plywood’s surface hardness. “The remaining veneer layers in plywood lay-up did not increase the surface hardness significantly. On the contrary, the higher number of densified layers in the plywood helped to increase the screw withdrawal capacity,” said Kers.
This increase, according to the professor, can be attributed to the compressed fibres and compact structure of the densified wood, which enhance the connection between the screw threads and the wood: “The effect is more noticeable when there are more densified layers in the plywood. The densified veneer surface layers of the plywood have a higher flexibility and rigidity than those of the undensified veneer of the same thickness. The densified veneers have a lower surface roughness, but this does not affect the bonding quality between the undensified and densified veneers.”
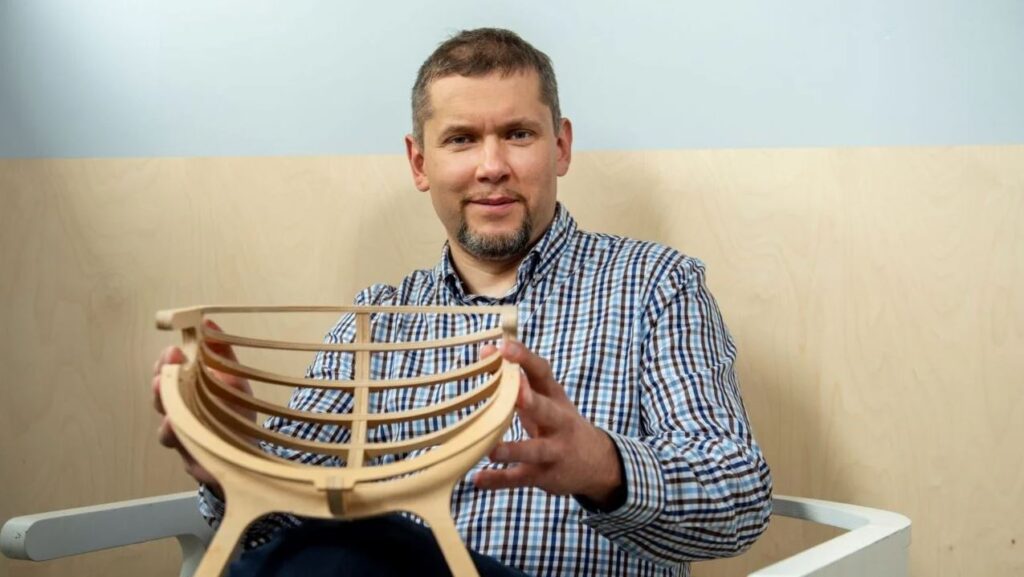
What material has the greatest load carrying capacity?
According to Kers, if there are no dimensional restrictions on the thickness of the material and the plywood works under bending loads, undensified veneers should be used for plywood production. “The undensified plywoods also provide greater load carrying capacity due to their greater thickness and rigidity.”
When densification is used as an additional step in the production of plywood, the material cost of the densification process, shrinkage and the problems related to dimensional stability also increase the overall material cost. As a result, plywood with only densified surface veneers has significant advantages over plywood made with fully densified veneer layers.
“Veneer densification is more effective when working with construction materials under tensile and compressive loads, as strength in these situations is inversely related to thickness. By using densified veneers only in face layers of plywood, it is possible to enhance resistance to bending loads similarly to plywood with fully densified layers, but with reduced material usage. Optimising the number of layers can help minimize the loss of load carrying capacity. With this minor adjustment, it is possible to produce thinner plywood or plywood with improved flexural strength, load carrying capacity, and a higher modulus of elasticity compared to plywood made from undensified veneers of the same thickness, all without altering the production process,” Kers stated.
According to Kers, the project demonstrated how, by densifying low-quality hardwood and combining it with different layers, undervalued black alder, grey alder, and aspen can be successfully used in wood composite materials. “And peeling leftover from veneer production can be successfully used in the production of laminated veneer lumber!”
The research team included, in addition to Professor Jaan Kers, Professor Heikko Kallakas, researcher Anti Rohumaa, engineer Kärt Kängsepp, PhD students-junior researchers Tolgay Akkurt and Catherine Kilumets, and technician Margus Kangur.
This article was originally published on the webpage of Tallinn University of Technology (TalTech) in their publication TRIALOOG. Author: Kaire Uusen.
If you think trees are just standing still, think again! Dive into our next article to see how cutting-edge technology is monitoring forests and keeping our woodlands thriving for generations to come. Read more about how Tartu Observatory helps Ukraine to develop monitoring systems for forests and water-bodies!